Wire gauge plays a vital role in assessing wire thickness and conductivity across diverse uses. Understanding AWG aids in selecting suitable wires. Balancing factors like current capacity and voltage drop is crucial. Exploring these challenges underscores the significance of AWG decisions in electrical applications.
American Wire Gauge
Gauge No. | Inches | Millimeters |
---|---|---|
7/0 | 0.651300 | 16.54 |
6/0 | 0.580049 | 14.73 |
5/0 | 0.516549 | 13.12 |
4/0 | 0.460000 | 11.68 |
3/0 | 0.409642 | 10.40 |
2/0 | 0.364797 | 9.266 |
1/0 | 0.324861 | 8.251 |
1 | 0.289297 | 7.348 |
2 | 0.257626 | 6.544 |
3 | 0.229423 | 5.827 |
4 | 0.204307 | 5.189 |
5 | 0.181941 | 4.621 |
6 | 0.162023 | 4.115 |
7 | 0.144285 | 3.665 |
8 | 0.128490 | 3.264 |
9 | 0.114424 | 2.906 |
10 | 0.101897 | 2.588 |
11 | 0.090742 | 2.305 |
12 | 0.080808 | 2.053 |
13 | 0.071962 | 1.828 |
14 | 0.064084 | 1.628 |
15 | 0.057068 | 1.450 |
16 | 0.050821 | 1.291 |
17 | 0.045257 | 1.150 |
18 | 0.040303 | 1.024 |
19 | 0.035891 | 0.9116 |
20 | 0.031961 | 0.8118 |
21 | 0.028462 | 0.7229 |
22 | 0.025347 | 0.6438 |
23 | 0.022572 | 0.5733 |
24 | 0.020101 | 0.5106 |
25 | 0.017900 | 0.4547 |
26 | 0.015941 | 0.4049 |
27 | 0.014196 | 0.3606 |
28 | 0.012641 | 0.3211 |
29 | 0.011258 | 0.2860 |
30 | 0.010025 | 0.2546 |
31 | 0.008928 | 0.2268 |
32 | 0.007950 | 0.2019 |
33 | 0.007080 | 0.1798 |
34 | 0.006305 | 0.1601 |
35 | 0.005615 | 0.1426 |
36 | 0.005000 | 0.1270 |
37 | 0.004453 | 0.1131 |
38 | 0.003965 | 0.1007 |
39 | 0.003531 | 0.08969 |
40 | 0.003145 | 0.07988 |
41 | 0.002800 | 0.07112 |
42 | 0.002494 | 0.06335 |
43 | 0.002221 | 0.05641 |
44 | 0.001978 | 0.05024 |
45 | 0.001761 | 0.04473 |
46 | 0.001568 | 0.03983 |
47 | 0.001397 | 0.03548 |
48 | 0.001244 | 0.03160 |
49 | 0.001108 | 0.02814 |
50 | 0.000986 | 0.02504 |
51 | 0.000878 | 0.02230 |
52 | 0.000782 | 0.01986 |
53 | 0.000697 | 0.01770 |
54 | 0.000620 | 0.01575 |
55 | 0.000552 | 0.01402 |
56 | 0.000492 | 0.01250 |
57 | 0.000438 | 0.01113 |
58 | 0.000390 | 0.00991 |
59 | 0.000347 | 0.00881 |
60 | 0.000309 | 0.00785 |
What is American Wire Gauge (AWG)?
American Wire Gauge (AWG) serves as a standard measure across North America for electrically conducting wire diameter. Balancing factors such as current capacity and conductivity is essential when utilizing AWG.
Challenges arise in choosing between thicker wires for higher current versus thinner wires for lower current applications. This emphasizes the critical impact of AWG decisions on electrical efficiency and safety in various settings.
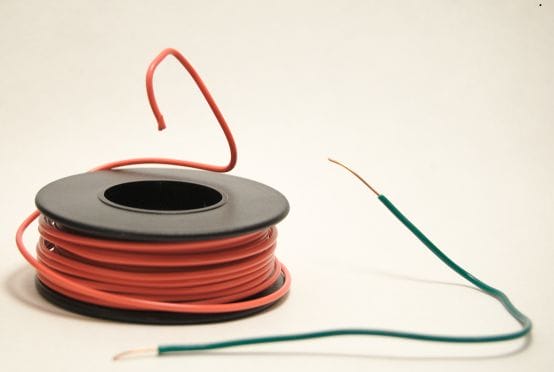
History of AWG
Originally developed in 1857 by the Browne & Sharpe wire gauge system, AWG was subsequently adopted as the standard for wire diameter measurement in the United States. Balancing historical context with modern applications reveals challenges in adapting AWG to contemporary electrical needs.
Understanding this evolution underscores the significance of AWG in ensuring compatibility and efficiency in electrical systems today.
AWG vs. Metric Wire Gauge
AWG is prevalent in the United States, whereas Metric Wire Gauge (SWG) is the standard in many other regions globally. Differentiating between these systems is crucial for international wire selection. Understanding these variations facilitates informed decisions but also presents challenges in standardizing practices across different wire gauge systems, impacting global manufacturing and compatibility in electrical applications.
AWG Conversion Chart
An AWG conversion chart facilitates the transformation of AWG sizes into diameters measured in inches or millimeters, and vice versa. AWG to Diameter Conversion provides guidance on calculating wire diameters from AWG sizes. Conversely, Diameter to AWG Conversion details how to determine the appropriate AWG size based on a given wire diameter.
Understanding these conversions is essential for accurately selecting wires based on specific electrical requirements, though challenges in precision and application compatibility may arise.
Common Uses of AWG Sizes
AWG sizes serve distinct purposes across applications: Lower AWG numbers signify thicker wires capable of handling high currents, ideal for power lines. Conversely, higher AWG numbers denote thinner wires suited for low current tasks, such as signal transmission in electronics.
Balancing between these factors involves considerations of efficiency and safety, emphasizing the critical role of AWG selection in optimizing electrical performance and reliability.
Practical Examples
In everyday and industrial settings, AWG sizes fulfill specific roles:
AWG 10 supports household electrical wiring, ensuring robust current handling.
AWG 24 is prevalent in data cables and telecommunications, prioritizing data transmission efficiency. Balancing these applications involves weighing factors like conductivity and space constraints, highlighting the critical need for accurate AWG selection to optimize performance and reliability in diverse electrical environments.
Choosing the Right AWG Size
When choosing the right AWG size, several key factors come into play:
Current carrying capacity determines the amount of electrical current a wire can safely conduct without overheating.
Voltage drop considerations involve minimizing the loss of voltage over distances, crucial for maintaining equipment efficiency.
Environmental conditions such as temperature and moisture affect wire durability and longevity.
Balancing these factors is essential; opting for thicker wires (lower AWG numbers) enhances current capacity but may increase costs and installation complexity. Thinner wires (higher AWG numbers) reduce material costs and space requirements but may compromise on current carrying capability and voltage drop performance. Careful consideration of these tradeoffs ensures optimal performance and reliability in electrical systems.
Conclusion
Understanding the AWG conversion chart is crucial for electrical professionals. It promotes safety, efficiency, and compatibility across applications. By navigating tradeoffs like wire thickness and conductivity, practitioners can optimize performance and mitigate challenges in electrical installations, underscoring the chart’s vital role in informed decision-making.
FAQs.
What is AWG (American Wire Gauge)?
AWG is a standardized system used in North America to measure the diameter of electrically conducting wires.
How does AWG compare to Metric Wire Gauge (SWG)?
AWG is widely used in the United States, while SWG is common in other parts of the world. They differ in how wire diameters are measured and categorized.
Why is AWG important in electrical applications?
AWG helps determine a wire’s current-carrying capacity, voltage drop, and suitability for specific environments, ensuring safety and efficiency in electrical systems.
How do you use an AWG conversion chart?
An AWG conversion chart helps convert AWG sizes to actual wire diameters in inches or millimeters, and vice versa, aiding in wire selection and compatibility.
What factors should be considered when choosing an AWG size?
Factors include current requirements, voltage drop limitations, environmental conditions, and space constraints, all of which impact wire performance and safety.